We study linear and nonlinear structural dynamics of mechanical systems from both theoretical and experimental standpoints. The focus of our research group is twofold:
- Prediction of dynamic phenomena of mechanical systems by analytical, computational, and experimental methods,
- Utilization of dynamic phenomena, where the dynamical characteristics of mechanical systems are utilized for generating something useful.
We extensively use computational methods for the analysis, design, and optimization of mechanical systems.
Ongoing projects
Magnetic-force induced vibrations of electric machines
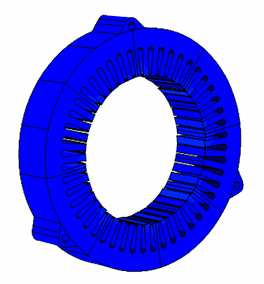
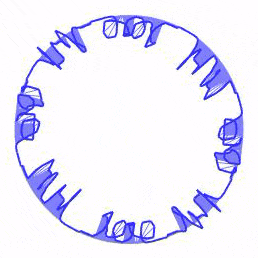
Rotating electric machines have been widely used for moving components of various mechanical structures, the representative of which is the traction drive of electric vehicles. The stationary parts of the electric machines, which are called stators, are subject to traveling-wave type electromagnetic force generated at the air-gap between the rotor and stator (Fig. 1). This produces undesirable oscillatory elastic deformation of the stator core (Fig. 2), which may be transmitted to other mechanical components or the surrounding environment in the form of acoustic noise. Based on accurate vibration prediction methods of electric machines (Refs. [1,2]), we are investigating such phenomena, by using both numerical and experimental methodologies.
References
[1] A. Saito et al. Efficient forced vibration reanalysis method for rotating electric machines, J. Sound Vib. 2015. [link]
[2] A. Saito et al. Empirical vibration synthesis method for electric machines by transfer functions and electromagnetic analysis, IEEE Trans. on Energy Conversion, 2016. [link]
Dynamics of mechanical structures involving mechanical contacts
– Systems with bolted joints
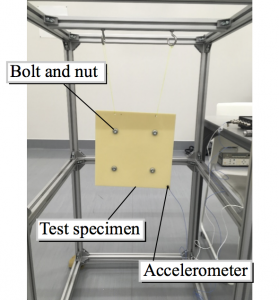
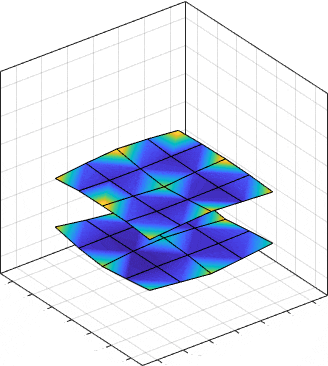
Mechanical structures consist of multiple components where the components are assembled by various methods such as welding, adhesives, and bolted joints. In particular, we work on understanding how bolted joints affect the dynamic characteristics of structures made of plastics, which are nowadays widely used for mechanical components. Experimental modal analysis and numerical methods such as finite element method are utilized to model and predict the dynamics of such structures.
References
[1] A. Saito and H. Suzuki, “Dynamic Characteristics of Plastic Plates with Bolted Joints”, Journal of Vibration and Acoustics, 2019. [link]
– Systems with intermittent contact
References
[1] K. Noguchi, et. al, Experimental and Numerical Investigations on Two Degrees of Freedom Piecewise-linear Nonlinear Systems with Gaps under Harmonic Excitation, IDETC2019, No. IDETC2019-97319, Anaheim, California, USA, August 2019.
[2] A. Saito. Nonlinear resonances of chains of thin elastic beams with intermittent contact, Journal of Computational and Nonlinear Dynamics, 2018. [link]
Inverse identification of damage using modal parameters
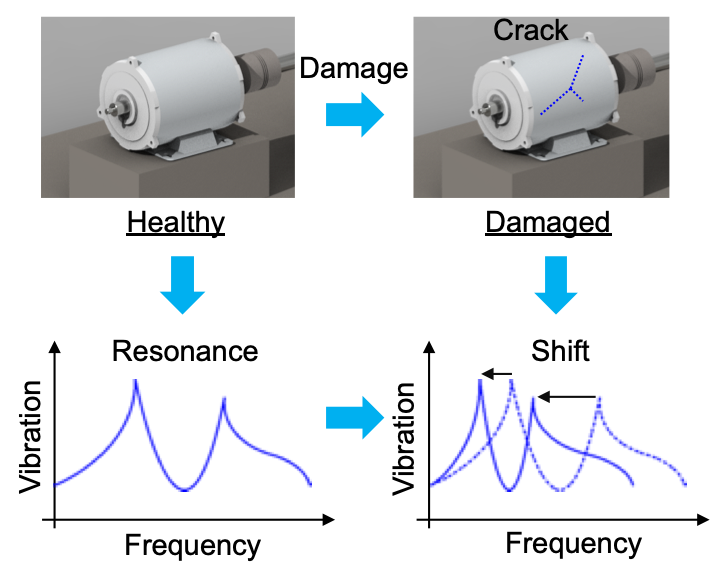
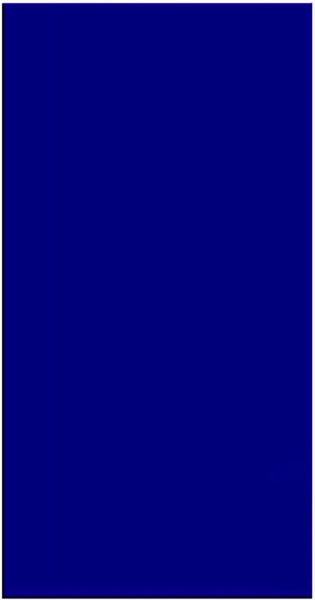
Structural damage identification is necessary to maintain the safety of mechanical structures. Vibration-based identification method has received increased attention over the past few decades because modal parameters can be obtained by experimental modal analysis relatively easily. In this project, an optimization-based inverse damage identification framework is developed and its applicability to general mechanical structures with various damage types is investigated. We are currently focusing on the development of algorithm to identify the location and length of a crack based on optimization methods using modal parameters [2]. Furthermore, we apply topology optimization and the concept of lasso regularization to identify the topology of the damage based on modal parameters[1,3].
References
[1] R. Sugai, A. Saito and H. Saomoto, “Damage Identification using Static and Dynamic Responses based on Topology Optimization and Lasso Regularization”, IDETC-2020, DETC2020-22279, Virtual conference (St. Louis MO, USA), August 2020.
[2] J. Isshiki, R. Sugai and A. Saito, ”Development of Crack Identification Method based on Finite- Element Model Updating and Inverse Eigenvalue Analysis”, ACSMO-2020, M3B-3, Seoul, Korea (online), November 2020.
[3] R. Sugai, A. Saito and H. Saomoto, ”Damage Identification using Topology Optimization with Lasso Regularization”, ACSMO-2020, W1A-2, Seoul, Korea (online), November 2020.
Experimental modal analysis
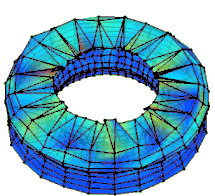
In order to understand the vibration phenomena of elastic media, experimental modal analysis has been widely used to extract modal properties of objects including resonant frequencies, mode shapes, and damping ratios. These quantities reflect mechanical properties of the object such as density, elasticity, and geometry, for instance. It means that we can develop indirect measurement methods of such properties by appropriately utilizing the functional relationships between the modal properties and the mechanical properties. In order to use modal parameters for such purposes, we are developing accurate modal parameter estimation methods. Recent development involves a time-domain modal parameter extraction method that uses the concept of Dynamic Mode Decomposition (DMD)[1]. DMD is a model order reduction method originally developed for fluid dynamics area, which can extract not only frequencies but also damping ratios of dominant components in the measured signals. In our research it is used for the extraction of modal parameters of structures.
References
[1] A. Saito and T. Kuno, ”Data-driven Experimental Modal Analysis by Dynamic Mode Decomposition”, Journal of Sound and Vibration, 481, 115434 (17 pages), 2020. [link]
Other ongoing topics
-
- Image-based experimental modal analysis
- Energy harvesting
- Anisotropy identification
- Damage detection using vibration data
- Meta-structures using additive manufacturing methods